Strong Screening Capacity Roll Crusher Machine 168-490 TPH Safe
Operation
Crushing Principle
The Roll Crusher Machine uses a single motor to drive the single
shaft to rotate and push the material to move forward along the
roll surface. The material is quickly dispersed and layered under
the same thickness screening characteristics of the inclined roll
surface (feeding section). The materials smaller than the gap
between the roller shafts are subject to their own gravity and the
rotating force of the roller shafts. They fall through the gap
between the roller shafts (adjust and determine the gap before
leaving the factory according to customer needs). The materials
larger than the gap between the roller shafts remain on the roller
shaft surface and continue to move forward, falling into the jaw
crusher or other crushers, so as to achieve the purpose of debris
separation and ore feeding.
Equipment Characteristics
1. The Roll Crusher Machine is mainly composed of frame, lining
plate, reduction motor, roller shaft assembly, bearing, bearing
seat, etc.
2. The Roll Crusher Machine is XCDRS1010, with a surface width of
1000mm and 10 roller shafts. The adjustable range of roller shaft
clearance is 25-100mm.
3. A single motor drives a single shaft to rotate. This equipment
has ten motors with a power of 3-5.5 kW.
4. The feed side length of this Roll Crusher Machine is less than
500 mm, and the throughput is 168-490 tons per hour.
Technical Reference Data
Model | Roll surface width (mm) | Number of axes | Throughput (t/h) | Feed side length (mm) | Roll shaft clearance (mm) | Screening efficiency (%) | Installed power | Flap drive push rod (optional for for electro hydraulic users) |
Power (kw) | Number | Model | Thrust (kgf) | Power (w) |
XCDRS1008 | 1000 | 8 | 140-385 | ≤500 | 25-100 | 80 | 2-4 | 8 | DT or DTY | 300 | 370 |
XCDRS1010 | 10 | 168-490 | 85 | 3-3.5 | 10 |
XCDRS1012 | 12 | 210-595 | 90 | 12 |
XCDRS1408 | 1400 | 8 | 294-700 | ≤700 | 35-120 | 80 | 8 | DT or DTY | 500 | 750 |
XCDRS1410 | 10 | 364-896 | 85 | 3-7.5 | 10 |
XCDRS1412 | 12 | 455-1050 | 90 | 12 |
Application in Debris Sorting
Principle:
A roller screen consists of a series of cylindrical shafts or
rollers that are arranged in a parallel configuration. These
rollers are equipped with screening elements, which allow for the
passage of particles of a certain size. The material to be sorted,
in this case, soil and rocks, is fed onto the rollers and moves
along their length due to the rotational motion of the shafts. As
the material travels across the rollers, particles smaller than the
screening elements pass through, while larger particles are
retained and transported to the end of the roller screen.
Effectiveness:
The effectiveness of a roller screen for soil and rock sorting is
determined by several factors:
Particle Size Separation: The screening elements on the rollers are carefully designed to
allow particles of a specific size to pass through. By adjusting
the spacing and configuration of the screening elements, the roller
screen can effectively separate the material into different size
fractions. This allows for the precise classification and sorting
of soil and rocks based on their particle size.
Scalping and Removal of Oversized Material: Roller screens are particularly effective in scalping
applications, where they remove the coarsest fractions or oversized
rocks from the material stream. The screening elements are designed
to retain larger particles, preventing them from passing through.
This helps to improve downstream processes, reduce the load on
crushers or conveyors, and ensure the desired size distribution of
the sorted material.
Handling High Volumes of Material: Roller screens are capable of handling high volumes of material
due to their robust design and efficient material transport
mechanism. The rotational motion of the shafts and the inclination
of the rollers facilitate the movement of the material along the
length of the roller screen, allowing for continuous and efficient
sorting operations.
Durability and Low Maintenance: Roller screens are typically constructed with sturdy materials and
components, ensuring durability and longevity even in demanding
environments. They are designed to withstand the abrasiveness and
impact of soil and rocks, minimizing the need for frequent
maintenance or replacement.
Our History
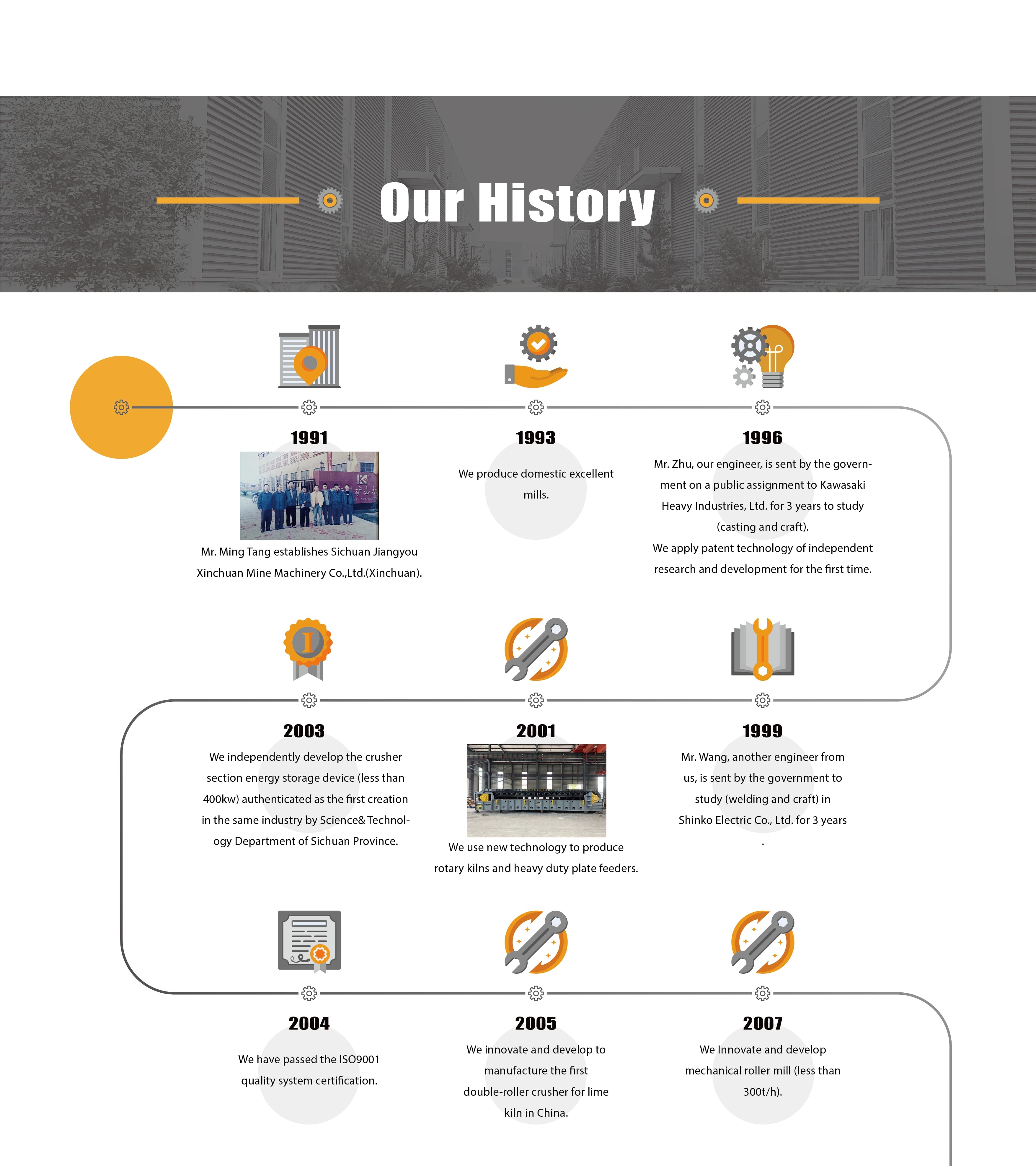
